One of our very friendly customers asked if he could get some pictures of his custom card holder being made. Of course we accepted his proposal, but perhaps took it a bit too far when we decided to document every single step. So please excuse the myriad of pictures in this post.
This shows just how many steps something as simple as a card holder goes through and hopefully it also shows some of the skill that goes into it. It's not done on an assembly line going from person to person performing the same task day in and day out. The wallet is made from start to finish by the same person. We do this because we're dedicated to making good, quality products.

We're making a double card holder in natural harness leather from our German tannery. This is available as a custom order currently. The harness leather is an undyed leather that has been stuffed with wax, oils and fats creating a leather with a beautiful pull up that ages very nicely.


The cardboard pattern is traced onto the leather using a round awl.


In this case we're cutting the leather using an old George Barnsley knife that has been converted into a clicking knife with a fine point.

First the exposed edges are sanded dry,

After which we wet the edges with a mix of glycerin and water before sanding the edges again while they're damp.

With a small edge beveler the edges are rounded.

The beveled edges are then burnished using our own wax formula. This seals the edge and gives it a slight shine. This step requires patience and skill.

In order to create a neat edge on the finished wallet the lower part of the central piece is skived in the bottom. We're skiving on an old litho stone, as the knife does dig into the surface and it doesn't dull the blade.

The backside is also burnished using a bone folder and another burnishing mixture that we make

In order to create a tight fold we first cut a shallow groove.

The groove allows the french edge skiver to remove a bit more material. You don't want to cut away too much material, but enough to get a tight fold.

The card holder can now be folded properly


The wallet is glued together using a water based glue in two steps. It could probably be done in one go, but it gives a greater sense of security because we want it folded tightly.

The seam allowance is marked using a divider.

The pricking irons set the stitches. They help you keep the angle that we want on our stitches

We mostly use prewaxed threads, but this thread needs a bit of extra wax, so we add our own thread wax by running the thread through the wax.

Running the thread through some heavy canvas removes any wax cakes on the thread and it helps it set by generating a bit of friction.

With the stitches set we pierce every hole using a sharp awl. No machines involved here.

One length of thread with a needle attached in each end creates what is known as the saddle stitch.

With the sewn card holder still in place in the sewing clam the edges are trimmed. We use our paring knife to level the edges.
More sanding. Dry and wet.

Edges are beveled to create a smooth and round edge. You'll notice that the stitches are slanted and sit at an angle. The look can easily be replicated by a sewing machine, but the durability of the saddle stitch cannot.

One of the most important steps is a good burnish. We again use our own wax blend and rarely use any edge dyes and never any edge paints.

The result being a smooth edge with as slight shine. The transformation is always incredible. You'll notice the middle piece being tapered towards the end where it was skived.

By tapping down the seams using a smooth faced hammer you avoid any unnecessary wear and tear on the stitches. Plus it improves their appearance.

As a finishing touch we give it a bit of our own conditioner.

Finally a good scrubbing with a horsehair brush removes any excess wax and conditioner.

Et voila.
We work closely with a German tannery that makes some of the most interesting leathers in the world. It's like a piece of history in working order. Here's a small walk-through of some of the processes that goes into a piece of leather.




















All the clothes are from my personal wardrobe, but if you want to know more about them or if you have a question, just ask away, and I'll try to fill you in. I'm very proud of the pictures alone, and I'm so proud of the fact that some major sites wanted to share them, and the reception that they've had from people has been overwhelming.
I didn't do this alone - by no means.
This is a short feature on a stuffed horse, two brothers, Danish modern and how crafts are almost extinct in our modern world
A stone's throw away from the main shopping street in Copenhagen there is a small saddler's shop called, Sadelmager Dahlman. It's a hidden gem with a great story, that needs to be told before it is too late and Dahlman is no more. At its prime Dahlman employed a lot of people and had some stuffed horses to exhibit their saddles, but now there are only two left, the brothers Frank and Erik Hendriksen and the horses have been donated to museums. They haven't employed any apprentices in recent times, so it's probably the end of the line for Dahlman.
Now I could go on and on about the great story and the great heritage of Dahlman, but in this case that isn't the interesting part. Of course it plays a huge part, but I don't find the equestrian side that exciting, though I can appreciate the craft and skills that it requires.
There are a few other saddlers in Denmark and some of them might be making belts and leather accessories, but what sets Dahlman apart from the others is their unique assortment. This is a direct result of their willingness to work together - what we today would call collaborate - with the architects, who would later go on and make Danish design very famous. Dahlman made leather work to their specifications and were generally very involved in the creation process. This resulted in leather work on furniture for many famous Danish designers such as Børge Mogensen and Arne Jacobsen, as well as more fashion related items such as a briefcase and a very special belt.



It was the very special belt and briefcase that was our goal on that early spring Saturday when we drove our bikes over to Dahlman's shop. We were greeted by Erik, who was the only one there, as Frank had some other business to attend to. At first he was quite apprehensive, but when he learned that we were very interested in his trade and his products, he more than willingly gave us a tour of Dahlman's legacy. We of course gladly inspected all their products with great care and inhaled that pleasant smell of good leathers that is everywhere in their shop. Erik also showed us all of their old tools which had been passed down by one generation of saddlers to the other. Some of the tools were over a hundred years old, and they looked well-used. Surprisingly they also had a lot of deadstock silver buckles that were used on the royal horse-drawn carriages, which are now used as belt buckles.



Now for the stuff that made us go to Dahlman's amazing shop. All of it has been made since the 1940's when it was developed together with Danish achitects like Kaare Klint, Poul Kühl and especially Erik Herlöw. It later became "comme il faut" among designers to wear these items.
First up, a pair of sandals. These are unlike most other Dahlman items sewn on an old Singer machine, but they are cut by hand. They are meant to be worn inside as a pair of very stylish slippers. If I remember correctly, they cost a 1000 kr ($200), unless you want them fitted for your wide or narrow feet, then they cost slightly more.


Secondly there is the breathtaking briefcase or attaché that was 30 kr (6 dollars in the 40's), when it was first made, and now comes to a staggering price of 24.000 kr (around $4.600), although it was on sale for a bit less. I'm not trying to justify the price, but you do get a very nice briefcase that has been completely handsewn, which takes a couple of days, in a very nice leather with custom made solid brass hardware. This is old world craftsmanship.
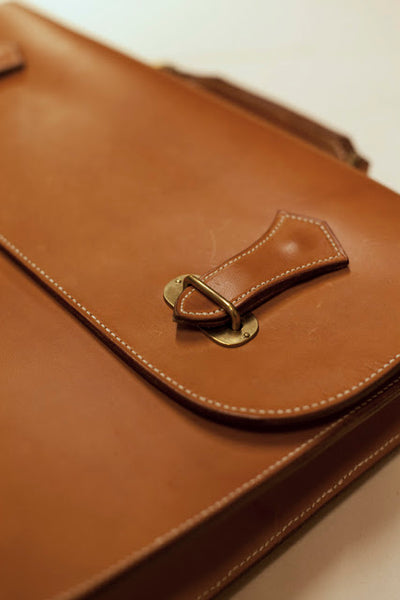




Lastly there is the belt that is commonly known as the "Architect belt" because it was worn by many of the Danish architects. In the beginning the belt came in natural only, but Arne Jacobsen wanted the belt in black, so he had the saddlers dye it black, so he could have it his way. If you talk to Erik about the belt, he'll refer to it as the "Saurmurhage bæltet" (in Danish) referring to the French origin of the hook stud used for the belt. The belt is normally made of 27mm wide vegetable tanned leather and again, every stitch is hand sewn using an awl and two needles. What you don't see, unless you inspect the back of the belt, is how each belt hole has drilled channel on the backside in order to make the hook go through the hole more easily.
To me this belt is iconic. Fantastic craftsmanship, great quality, beautiful details, minimalistic design and lastly a story like no other. The price isn't too bad either - around 1000 kr.
Thank you, Erik for taking your precious time to show us around your shop.